A Bukito 3D printer creates the likeness of actor Bruce Willis. Credit: Justin Sullivan / Getty
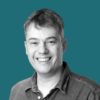
Most of the stuff we own is mass produced by machines. That’s why we can afford so much of it. Anything that’s professionally handmade is almost certainly a luxury product.
There’s one big exception, however: the homes we live in. Most of those are hand-made. The building materials may be machine-made, but the piece-by-piece, one-off process of construction is labour-intensive, time-consuming and frequently unpredictable.
There’s got to be a better way. Prefabrication is one approach, but that involves a trade-off between the size of the prefabricated components and their transportability. It also tends to constrain the materials that can be used and the variety of forms the building can take.
In the early 20th century, Thomas Edison wasted a lot of time and money on the development of the single-pour concrete house. Employing a set of re-usable moulds, he believed he could mass produce affordable housing for all. Unfortunately, the moulds were so complicated and expensive that it was easier and cheaper to build the traditional way. A sideline in concrete furniture also came to a predictably sticky end.
Edison’s single pour method didn’t just fail because of the practicalities; the principle was flawed too. A solid mass of concrete creates a structure that is virtually indestructible, but also unmodifiable – great for a bomb shelter, but not a home.
In an article for The Conversation, Seyed Ghaffar says that to successfully revolutionise house building we need to “automate and improve processes that have already been proven manually.”
Join the discussion
Join like minded readers that support our journalism by becoming a paid subscriber
To join the discussion in the comments, become a paid subscriber.
Join like minded readers that support our journalism, read unlimited articles and enjoy other subscriber-only benefits.
Subscribe