A Bukito 3D printer creates the likeness of actor Bruce Willis. Credit: Justin Sullivan / Getty
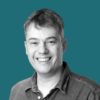
Most of the stuff we own is mass produced by machines. That’s why we can afford so much of it. Anything that’s professionally handmade is almost certainly a luxury product.
There’s one big exception, however: the homes we live in. Most of those are hand-made. The building materials may be machine-made, but the piece-by-piece, one-off process of construction is labour-intensive, time-consuming and frequently unpredictable.
There’s got to be a better way. Prefabrication is one approach, but that involves a trade-off between the size of the prefabricated components and their transportability. It also tends to constrain the materials that can be used and the variety of forms the building can take.
In the early 20th century, Thomas Edison wasted a lot of time and money on the development of the single-pour concrete house. Employing a set of re-usable moulds, he believed he could mass produce affordable housing for all. Unfortunately, the moulds were so complicated and expensive that it was easier and cheaper to build the traditional way. A sideline in concrete furniture also came to a predictably sticky end.
Edison’s single pour method didn’t just fail because of the practicalities; the principle was flawed too. A solid mass of concrete creates a structure that is virtually indestructible, but also unmodifiable – great for a bomb shelter, but not a home.
In an article for The Conversation, Seyed Ghaffar says that to successfully revolutionise house building we need to “automate and improve processes that have already been proven manually.”
A century on from Edison’s doomed attempt we might just be on the brink of getting it right:
“It’s often claimed that 3D printing – known in the trade as ‘additive manufacturing’ – will change the way we live. Most recently, a team from Eindhoven University of Technology announced plans to build the ‘world’s first’ habitable 3D printed houses…
“Additive manufacturing uses a combination of materials science, architecture and design, computation and robotics. Yet in some ways, it’s not as futuristic as it sounds. The simple approach of layer-wise construction… has already been practised for a long time in the construction sector, for example in conventional brick layering techniques.”
In fact, with 3D printing we might be able to go well beyond what even the most skilled human builders are capable of:
“When the printer and the feedstock have been properly set up, they will be able to produce full-size building blocks with a smart geometry which can take load without reinforcements. The shape stability of the truss-like filaments in these blocks is an essential part of printing, which provides strength and stiffness to the printed objects.”
Nature has all sort of cunning ways of creating light but strong structures – from the spider’s web to the bones of flying birds. The rapid, but precise, movements of 3D printers could allow us to draw inspiration from evolution, and extrude building materials to achieve great intricacy and efficiency.
Ghaffar believes that smart and automated construction methods could “revolutionise the industry within the next ten to 15 years”.
Will this make houses more affordable? It may well bring construction costs tumbling down – but, remember, not even a robot can make new land. Therefore, we’ll need policies to stop land monopolists from sucking up the value created by new technology.
That said, the automation of house building may make it harder for developers to manipulate land prices by manipulating the rate at which land with planning permission is built out. With robots greatly speeding up the pace of construction, there’ll be no excuse not to build new homes as fast as demand requires and planning policies allow.
One last thought: Though Edison’s poured concrete technology was misconceived, the prototype houses he built with it could be surprisingly beautiful. The developers of today’s new construction methods would be well advised to pay equally close attention to the aesthetics.
If you want the public to accept new development, then the golden rule is that it should make places better not worse.
Join the discussion
Join like minded readers that support our journalism by becoming a paid subscriber
To join the discussion in the comments, become a paid subscriber.
Join like minded readers that support our journalism, read unlimited articles and enjoy other subscriber-only benefits.
Subscribe